Ottimizzazione delle dimensioni del cancello e posizione in uno stampo a iniezione con pompa per lozione attraverso l'analisi del flusso dello stampo comporta un processo sistematico di simulazione, analisi e aggiustamenti di progettazione. Ecco una guida passo passo per ottenere questa ottimizzazione:
1. Definire obiettivi e criteri del progetto:
- Inizia definendo chiaramente gli obiettivi e i criteri per lo stampo a iniezione della pompa per lozione. Considera fattori quali la qualità delle parti, il tempo di ciclo, l'utilizzo dei materiali e i vincoli di costo.
2. Raccogliere dati sui materiali:
- Ottenere dati accurati sui materiali per la specifica resina plastica da utilizzare nel processo di stampaggio a iniezione. Ciò include l'indice di flusso di fusione (MFI), la viscosità, le proprietà termiche e altre caratteristiche del materiale.
3. Creazione del modello:
- Crea un modello 3D dettagliato della parte della pompa per lozione e dello stampo a iniezione, inclusa la cavità, il nucleo, i canali di raffreddamento e il sistema di canali. Assicurarsi che il modello rappresenti accuratamente le condizioni di produzione previste.
4. Impostazione della simulazione:
- Utilizzare il software di analisi del flusso dello stampo per impostare la simulazione. Definire i parametri del processo di stampaggio a iniezione, come pressione di iniezione, profili di temperatura e velocità di raffreddamento. Specificare le posizioni dei cancelli e le dimensioni iniziali dei cancelli.
5. Esecuzione iniziale della simulazione:
- Eseguire la simulazione del flusso dello stampo iniziale con le posizioni e le dimensioni del cancello scelte. Analizzare i risultati, inclusi tempo di riempimento, distribuzione della pressione, linee di saldatura e posizioni delle trappole d'aria. Identificare eventuali problemi o aree di miglioramento.
6. Analisi della posizione del cancello:
- Valutare l'idoneità delle posizioni dei varchi prescelti. Considera fattori come il riempimento equilibrato delle cavità, l'eliminazione di difetti estetici e la riduzione al minimo dell'impatto delle linee di saldatura. Modificare la posizione dei cancelli secondo necessità.
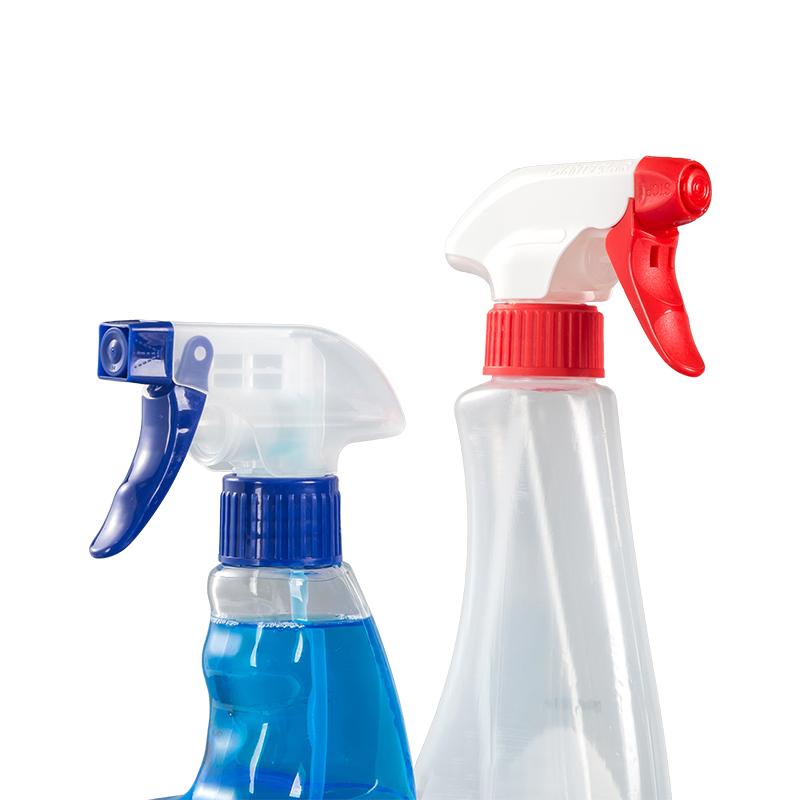
7. Analisi delle dimensioni del cancello:
- Analizzare l'effetto della dimensione del gate sul processo di iniezione. Aumenta o diminuisci gradualmente le dimensioni del punto di accesso nelle simulazioni successive per trovare la dimensione ottimale che bilanci tempo di riempimento, pressione e flusso di materiale senza causare difetti.
8. Selezione del tipo di cancello:
- A seconda dei risultati dell'analisi delle dimensioni del punto di accesso, scegliere il tipo di punto di accesso appropriato, ad esempio un punto di colata, un punto di accesso sul bordo o un punto di accesso a ventola. Il tipo di accesso influisce sul modo in cui il materiale entra nella cavità e può influire sulla qualità della parte.
9. Ottimizzazione del sistema Runner:
- Ottimizzare il design del sistema di canali per garantire una distribuzione uniforme del materiale in tutte le cavità. Regolare le dimensioni e le configurazioni dei canali per ridurre al minimo lo spreco di materiale e la caduta di pressione.
10. Analisi dei canali di raffreddamento:
- Valutare l'impatto della posizione e delle dimensioni del cancello sull'efficienza del raffreddamento. Assicurarsi che la configurazione scelta della porta non interferisca con l'efficacia dei canali di raffreddamento. Se necessario, regolare la posizione del canale di raffreddamento.
11. Simulazione iterativa:
- Eseguire simulazioni iterative, apportando aggiustamenti graduali alle posizioni e alle dimensioni dei cancelli in base ai risultati dell'analisi. Continuare a perfezionare il progetto fino a quando non vengono soddisfatti i criteri desiderati, come riempimento equilibrato e difetti minimi.
12. Convalida finale:
- Condurre un'analisi finale del flusso dello stampo per convalidare la dimensione e la posizione ottimizzate del cancello. Confermare che il progetto soddisfi gli obiettivi e i criteri di progetto predefiniti.
13. Documentazione e reporting:
- Documentare i risultati, inclusa la configurazione del cancello scelta, i dati di simulazione ed eventuali modifiche alla progettazione. Preparare un rapporto che riassuma il processo di ottimizzazione e i suoi risultati.